The Royal Victoria Building is a purpose-built clinical facility that forms part of the Western General Hospital in Edinburgh.
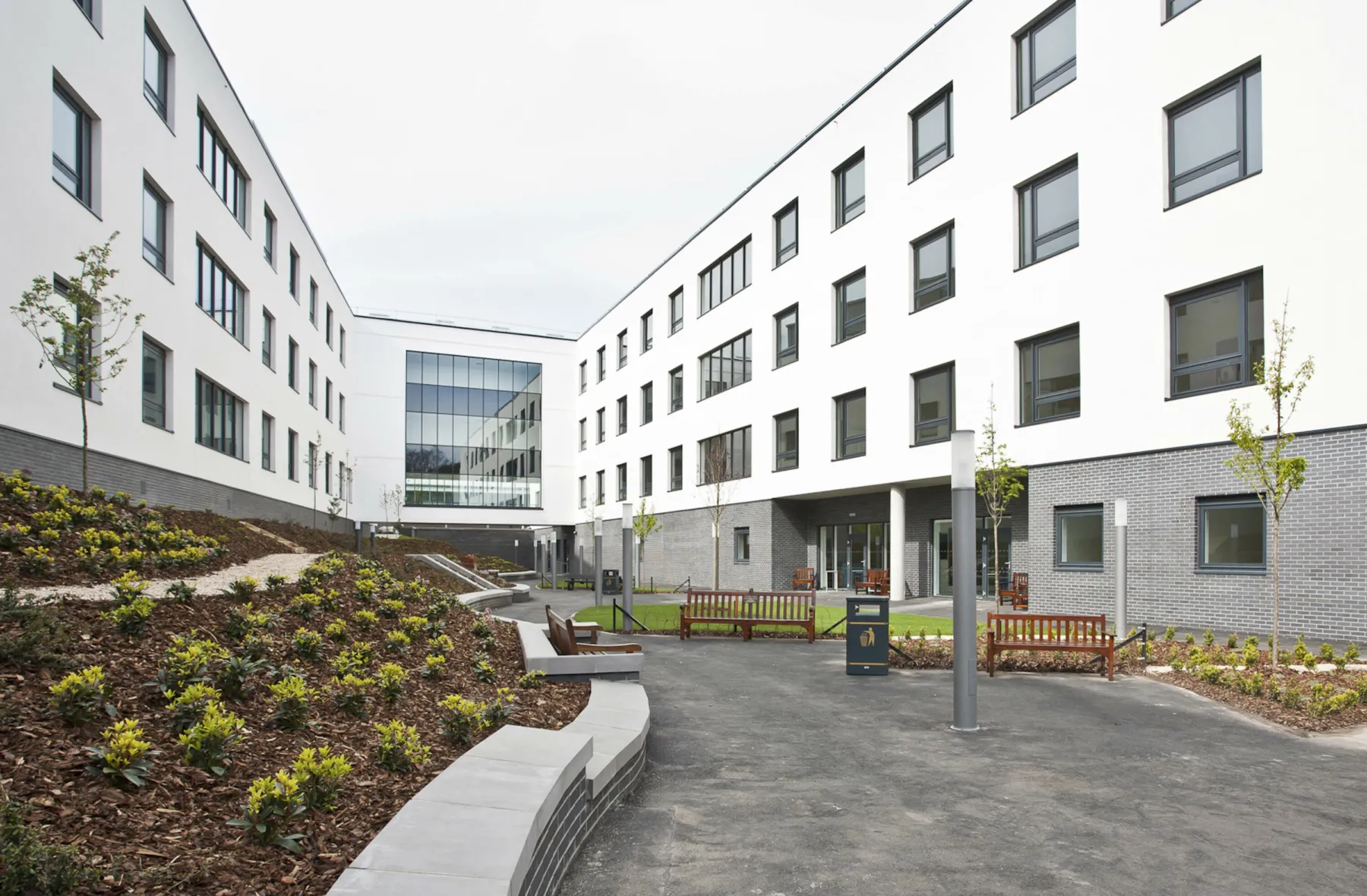
Four of its six wards are devoted to care of the elderly, with the remainder catering to rheumatology and dermatology patients and those requiring orthopaedic rehabilitation. There is also an assessment and rehabilitation centre for both day and outpatients.
Redundant buildings on the site were demolished to make way for the four-storey hospital wing, which contains 147 beds, all in single occupancy. A bridge links the new building to the existing Western General complex, meaning patients do not have to go outside to get to other parts of the hospital.
Additional facilities include a café and seating area on the ground floor with a central landscaped courtyard, creating a welcoming social area outside the ward environments.
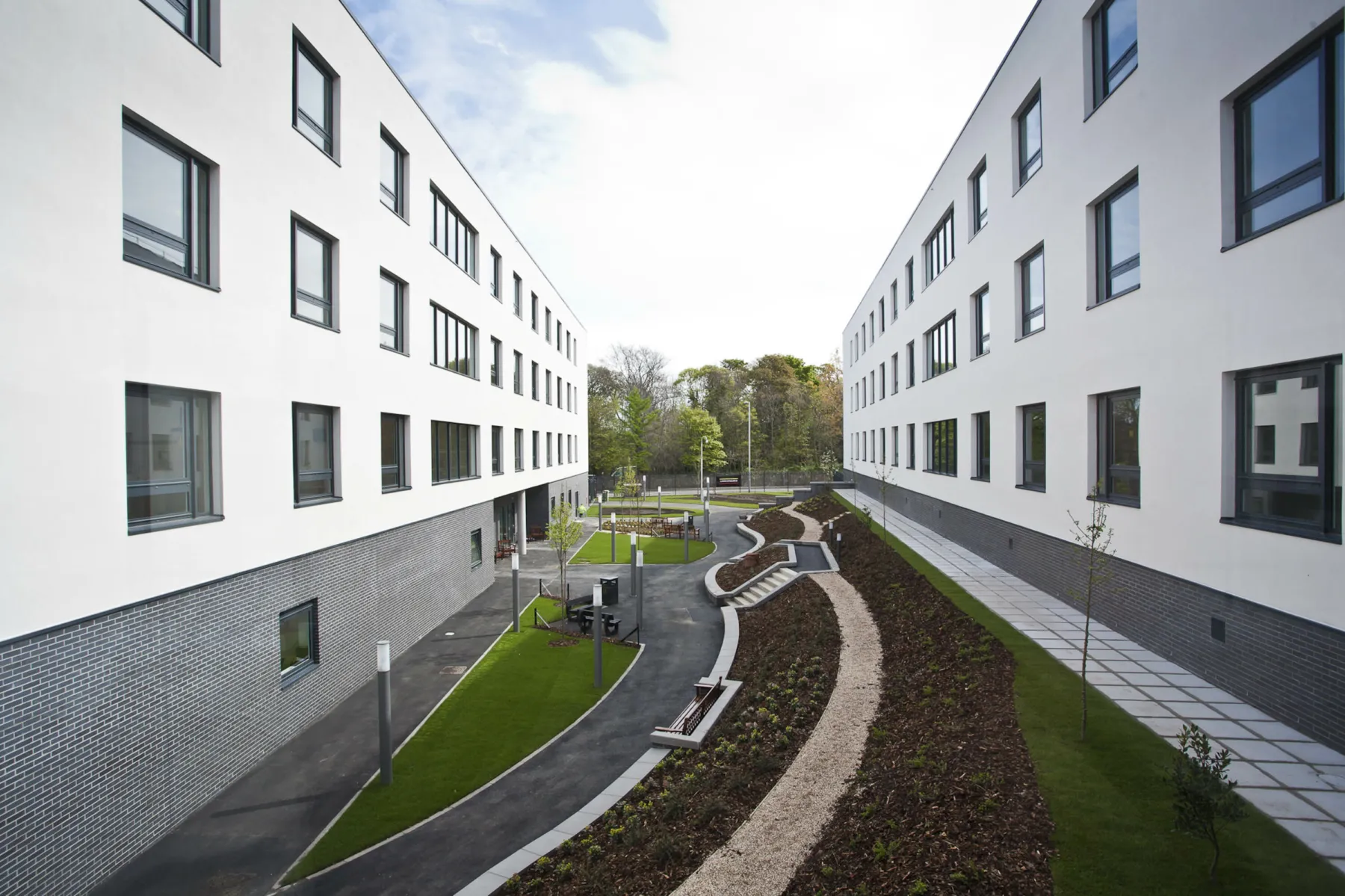
Project Director, NHS Lothian
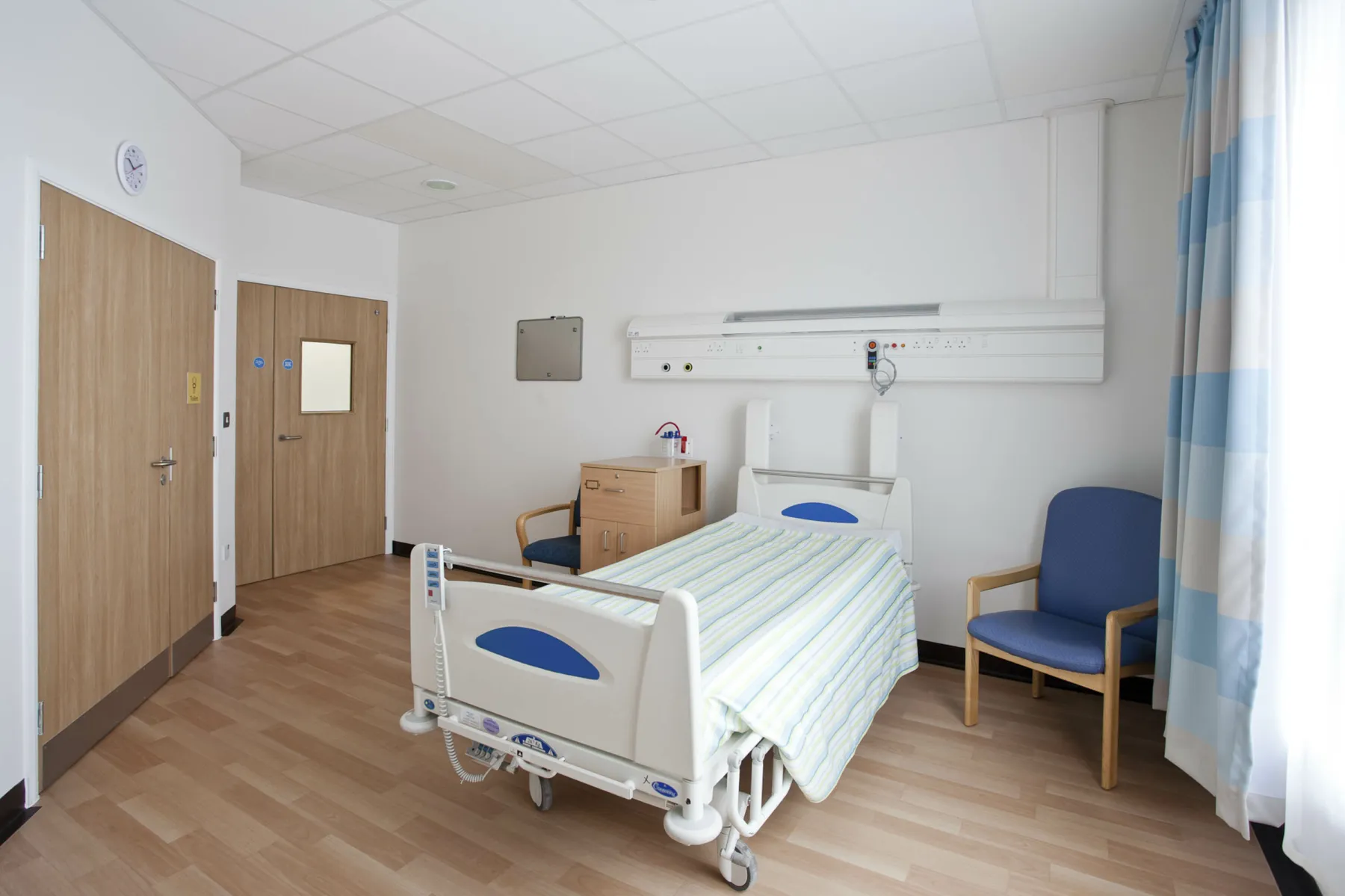
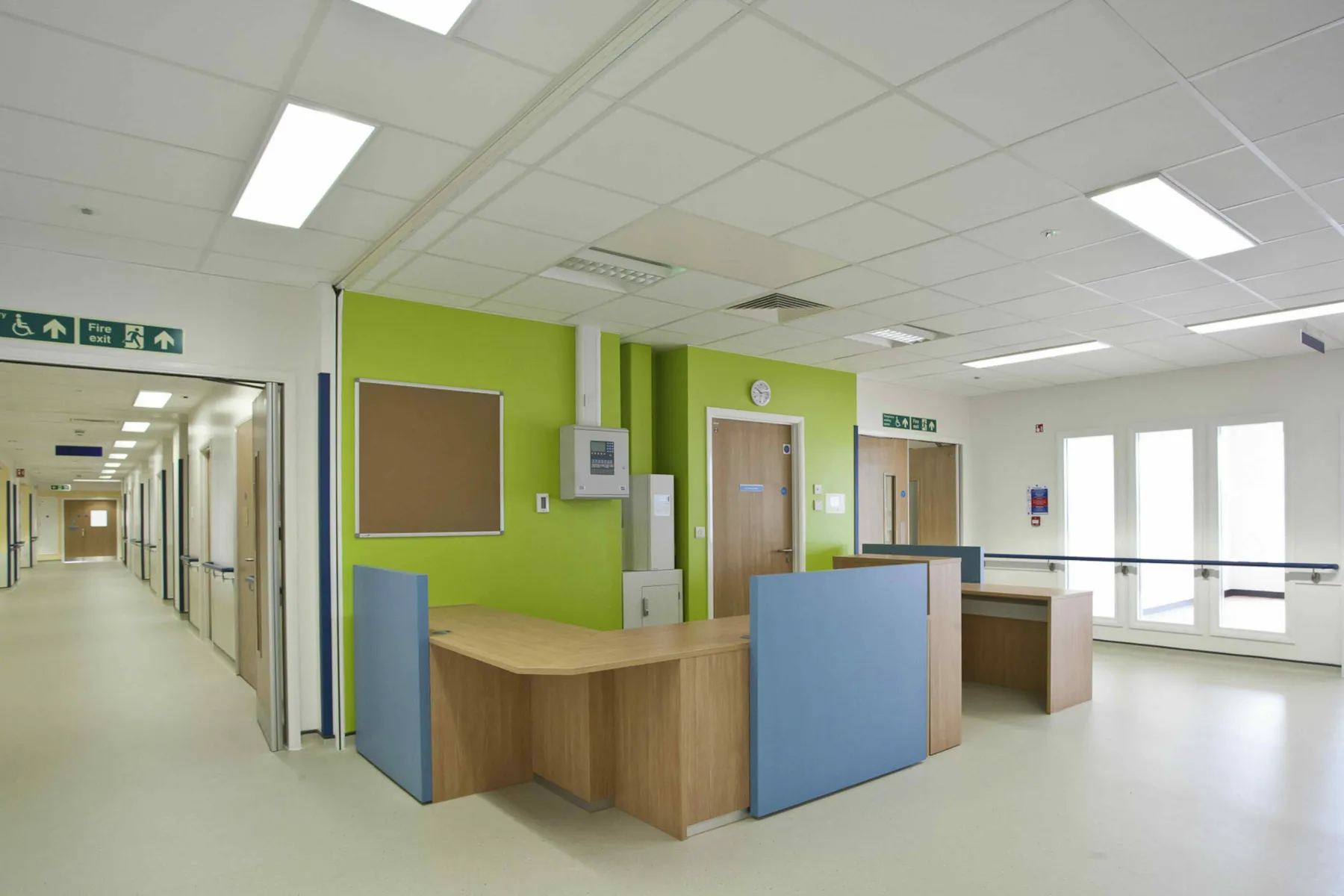
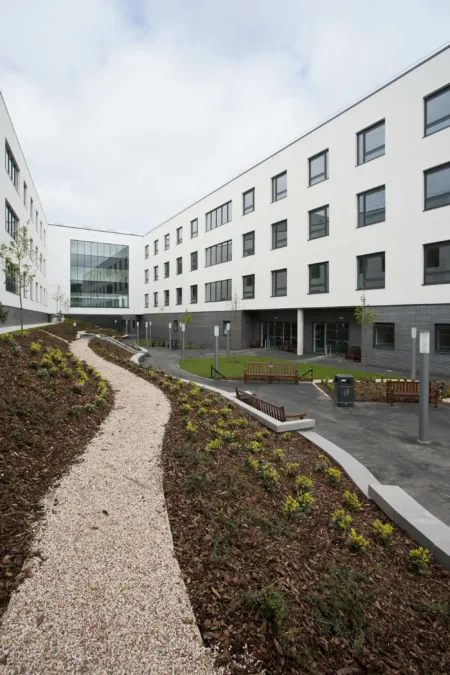
Healthcare facility design under the new HFS framework
The Royal Victoria Building was one of the first major projects to be built in the context of the Health Facilities Scotland (HFS) framework using a single source principal supply chain partner (PSCP).
With our extensive experience of the NEC3 contract process, we were able to accurately assess the costs under this new procurement model – involving an internal supply chain that does not necessarily go into open competition – while ensuring best value for the client.
Our value-for-money reports helped to secure approvals from NHS Lothian and the Scottish Government for the project to proceed.
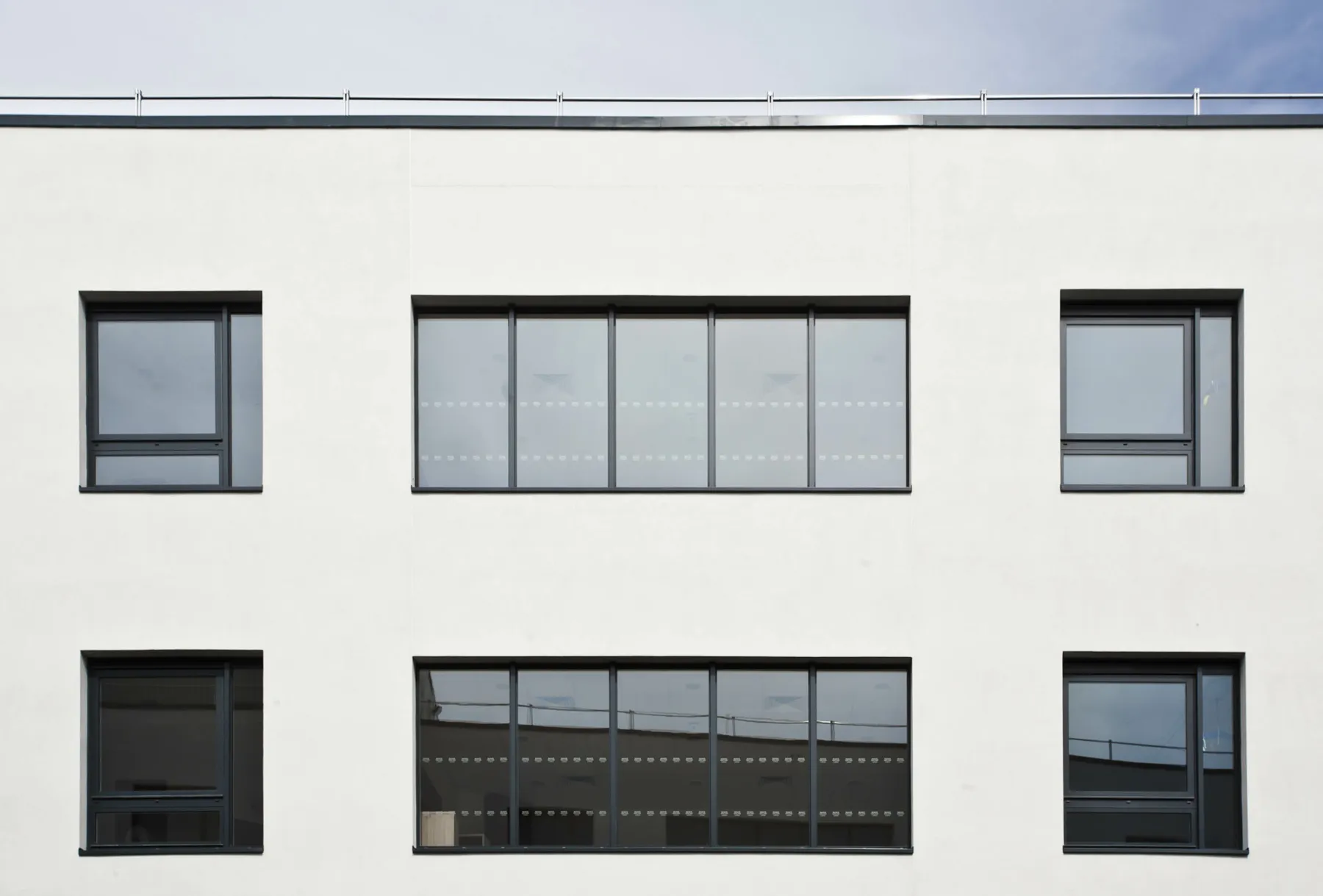
Hospital construction efficiencies
The structure of the building comprises an innovative non-cavity ‘warm wall’ concrete frame with a high-quality finish on the inside and insulation on the outer face. The design also made considerable use of prefabrication, with 55% of the components made off-site and delivered on a just-in-time basis ready to be craned into place.
Wall panels were pre-fitted with windows, obviating the need for glaziers to obtain weather-tightness, and bathroom pods for each of the 147 patient rooms were delivered to site plumbed and ready for connection to the building services. Flat slab soffits allowed easy installation and maintenance of services while also future-proofing the building for layout changes.
We were instrumental in proving the cost advantages of the concrete frame and the flat slabs, generally considered a more expensive option at the time. Moreover, by recommending a reduction in bedroom sizes, we achieved significant economic improvements with no impact on design or care function.
Other cost efficiencies included the addition of a Kemper automated water-flushing system for preventing Legionella which, after cost analysis, proved a fraction of the cost of the alternative – staff manually running taps – over the life span of the building.
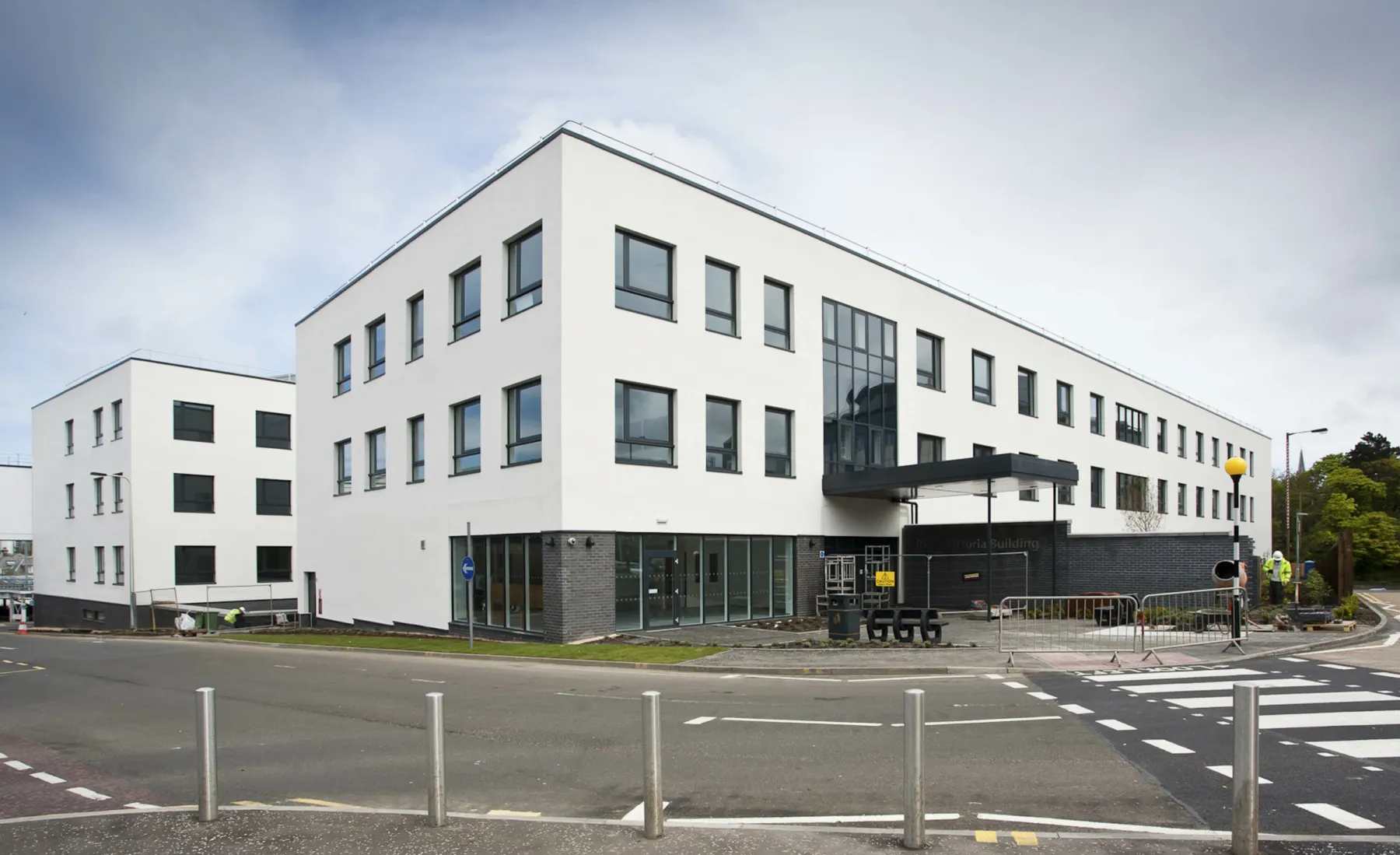
Sustainable outcome
The mass concrete frame delivers considerable thermal resistivity benefits to the building and, along with other efficiencies such as using the Western General’s local district heating system, photovoltaic cells on the roofs and wireless clinical care technology, the finished building obtained a BREEAM sustainability rating of ‘excellent’.
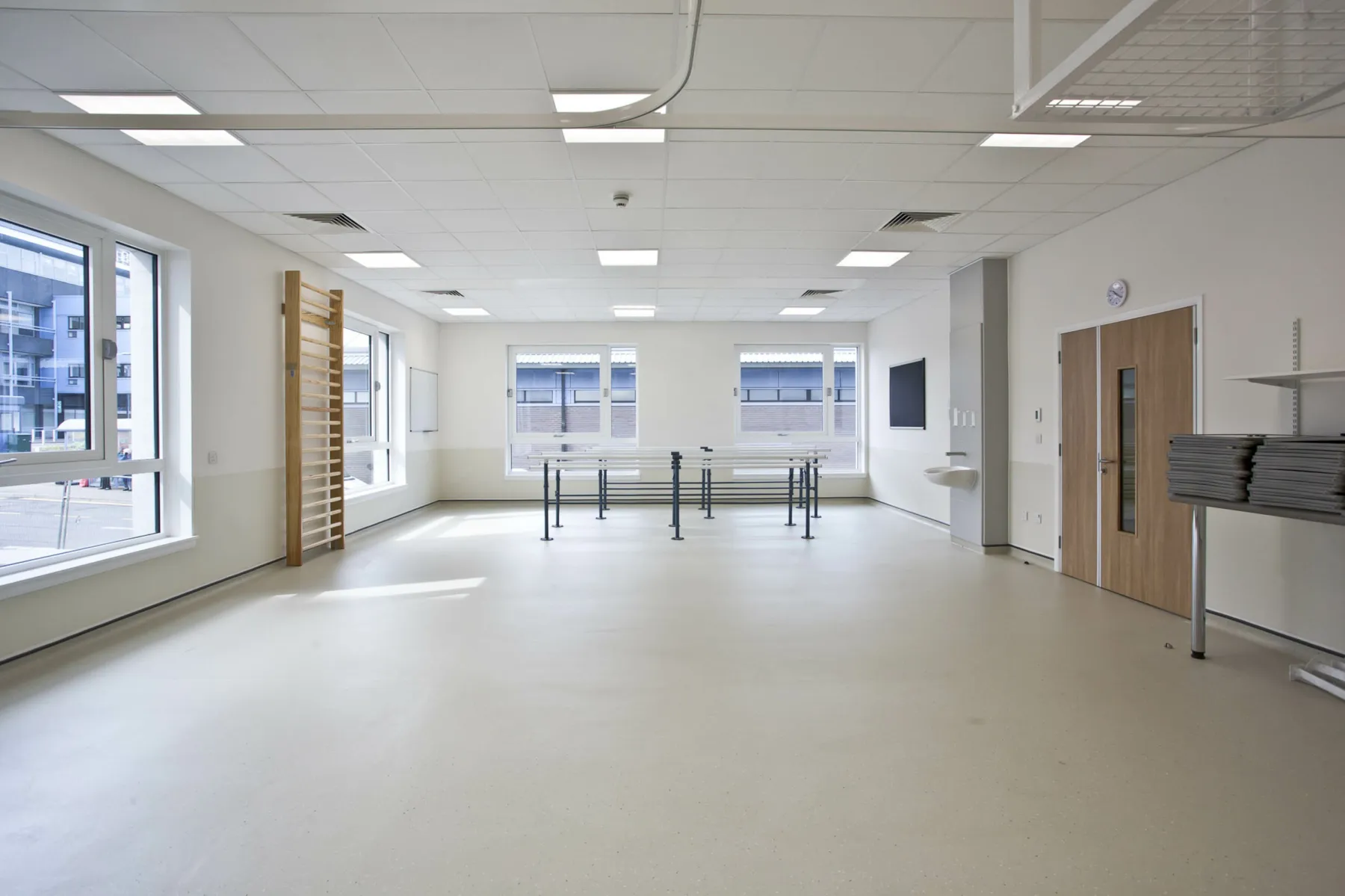
Credits
Architect Keppie Design
Contractor Laing O’Rourke
Structural Engineer Mott MacDonald
Services Engineer WSP
Quantity Surveyor Thomson Gray
CDM Coordinator Thomson Gray
Images David Stirling